-
- News
- Books
Featured Books
- smt007 Magazine
Latest Issues
Current IssueBox Build
One trend is to add box build and final assembly to your product offering. In this issue, we explore the opportunities and risks of adding system assembly to your service portfolio.
IPC APEX EXPO 2024 Pre-show
This month’s issue devotes its pages to a comprehensive preview of the IPC APEX EXPO 2024 event. Whether your role is technical or business, if you're new-to-the-industry or seasoned veteran, you'll find value throughout this program.
Boost Your Sales
Every part of your business can be evaluated as a process, including your sales funnel. Optimizing your selling process requires a coordinated effort between marketing and sales. In this issue, industry experts in marketing and sales offer their best advice on how to boost your sales efforts.
- Articles
- Columns
Search Console
- Links
- Events
||| MENU - smt007 Magazine
Reflow Your Solder and Your Data for Industry 4.0
June 11, 2019 | Nolan Johnson, I-Connect007Estimated reading time: 4 minutes
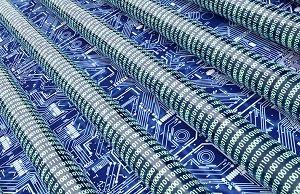
I-Connect007 Managing Editor Nolan Johnson recently spoke with KIC President and Founder Phil Kazmierowicz and Manager of Applications and Sales MB “Marybeth” Allen as they each transitioned into new roles in the KIC leadership team. The conversation ultimately turned to the current dynamics in the industry, particularly Industry 4.0 and streamlining processes.
To kick off the discussion, Johnson posed this question: "Generally speaking, there are two key parts to improving the efficiencies: faster, more accurate throughput, and increased uptime. From your perspective, watching the reflow process, what do you see as the greatest activity in the market for reducing the likelihood of the reflow process becoming the facility’s bottleneck?"
Kasmierowicz, Allen, and Johnson then delved into this question throughout a series of conversations and emails, which have been edited into the discussion that follows.
Faster, More Accurate Throughput
On the topic of throughput, Allen wrote, "A key component to an efficient manufacturing operation is optimization throughout the factory. One of the most effective ways to optimize is via software. Trial and error are a thing of the past. Optimization software not only assists with productivity but also defines and improves the process for the highest quality result. The optimization process for reflow starts in the early stages of setting up a product for solder reflow."
Allen continued, "Finding the correct recipe for a reflow oven to produce a PCB within the current, very tight, lead-free process windows could take significant amounts of both resources and time. Our predictive software tools assist a customer to find this recipe very quickly, likely in just two passes, which significantly reduces the amount of time just to set up a profile. In addition, our predictive software can give a customer an in-spec profile without even running a trial PCB. These two functions alone provide solutions for fast profiling for a high-quality product and within the specifications of the factory’s requirements, which include faster throughput, lower energy costs, and, of course, difficult and challenging assemblies with a variety of process windows between components and solder paste."
Phil Kazmierowicz explained the details. "Once the specification was defined mathematically, we invented the process window index, or PWI, which represents profile quality with a single number. In this way, oven recipes could be compared, allowing us to develop a software tool that we called Auto-Predict (now known as Navigator). This completely eliminates the guesswork as the software automatically finds an oven recipe that will process the board in spec.
"Our next group of products is used once you’re ready to start production," said Kazmierowicz. "How do you know boards or parts were processed correctly? We monitor the temperature and speed along the oven conveyor during production. We can say, ‘Based on these inputs, your output is still within the range that is going to work, and your boards are being processed in spec.’ Or we can identify problems, such as if zone eight and nine changed significantly. Our setup tools help the customer find the correct oven recipe and our automatic systems continuously monitor production. Simply trusting that no changes to the oven have occurred since you last attached thermocouples to your board or silicon—however long ago—is just not enough. Now, more customers want our monitoring capabilities."
Less Downtime
Allen summarized downtime as follows. "We all know that one of the worst things to hear in a factory is ‘downtime’ because this has a direct link to lost money/profits, delay in delivery, unhappy managers, owners, and most importantly, customers. With so much automation, there still tends to be the possibility of downtime in the reflow process. A reflow-related defect found by an AOI machine requires immediate action, for example. One of the investigative steps may be to run a profile to determine if there was any change in the reflow oven to determine if the fault is due to a process change, human intervention, or something else entirely."
"This downtime may be significantly reduced if a reflow process inspection (RPI) system is in use," explained Allen. "This RPI system will continuously monitor the conditions at the product level, provide the customer with data for each reflowed PCB, and notify the customer if a change is taking place and to what degree. If the current conditions are changing to a point where product entering the oven would not be in spec, a notification will take place and be automatically documented, and defective assemblies may be avoided. If there’s a defect found at AOI, you can rule out the oven.
Allen further detailed, "Planning for changeover downtime plays a role in optimization. With the knowledge of what products will be run on a given day, shift, oven, and their related profiles, the software can assist with the optimized plan to limit this changeover time in the reflow oven. An example is starting with SnPb assemblies and/or lower temperature profiles and working up to higher temperatures rather than the reverse, which takes time for oven cool down."
To read the full article, which appeared in the June 2019 issue of SMT007 Magazine, click here.
Suggested Items
Taiyo Circuit Automation Installs New DP3500 into Fuba Printed Circuits, Tunisia
04/25/2024 | Taiyo Circuit AutomationTaiyo Circuit Automation is proud to be partnered with Fuba Printed Circuits, Tunisia part of the OneTech Group of companies, a leading printed circuit board manufacturer based out of Bizerte, Tunisia, on their first installation of Taiyo Circuit Automation DP3500 coater.
Vicor Power Orders Hentec Industries/RPS Automation Pulsar Solderability Testing System
04/24/2024 | Hentec Industries/RPS AutomationHentec Industries/RPS Automation, a leading manufacturer of selective soldering, lead tinning and solderability test equipment, is pleased to announce that Vicor Power has finalized the purchase of a Pulsar solderability testing system.
AIM Solder’s Dillon Zhu to Present on Ultraminiature Soldering at SMTA China East
04/22/2024 | AIMAIM Solder, a leading global manufacturer of solder assembly materials for the electronics industry, is pleased to announce that Dillon Zhu will present on the topic: Ultraminiature Soldering: Techniques, Technologies, and Standards at SMTA China East. This event is being held at the Shanghai World Expo Exhibition & Convention Center from April 24-25.
AIM to Highlight NC259FPA Ultrafine No Clean Solder Paste at SMTA Wisconsin Expo & Tech Forum
04/18/2024 | AIMAIM Solder, a leading global manufacturer of solder assembly materials for the electronics industry, is pleased to announce its participation in the upcoming SMTA Wisconsin Expo & Tech Forum taking place on May 7 at the Four Points by Sheraton | Milwaukee Airport, in Milwaukee, Wisconsin.
Hentec/RPS Publishes an Essential Guide to Selective Soldering Processing Tech Paper
04/17/2024 | Hentec Industries/RPS AutomationHentec Industries/RPS Automation, a leading manufacturer of selective soldering, lead tinning and solderability test equipment, announces that it has published a technical paper describing the critical process parameters that need to be optimized to ensure optimal results and guarantee the utmost in end-product quality.