-
- News
- Books
Featured Books
- smt007 Magazine
Latest Issues
Current IssueBox Build
One trend is to add box build and final assembly to your product offering. In this issue, we explore the opportunities and risks of adding system assembly to your service portfolio.
IPC APEX EXPO 2024 Pre-show
This month’s issue devotes its pages to a comprehensive preview of the IPC APEX EXPO 2024 event. Whether your role is technical or business, if you're new-to-the-industry or seasoned veteran, you'll find value throughout this program.
Boost Your Sales
Every part of your business can be evaluated as a process, including your sales funnel. Optimizing your selling process requires a coordinated effort between marketing and sales. In this issue, industry experts in marketing and sales offer their best advice on how to boost your sales efforts.
- Articles
- Columns
Search Console
- Links
- Events
||| MENU - smt007 Magazine
Failures and Reliability in Soldering
July 9, 2019 | Michael Gouldsmith and Zen Lee, ThermaltronicsEstimated reading time: 3 minutes
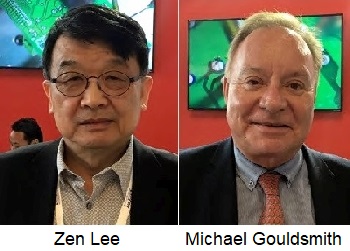
The definition of failure is “the lack of success in doing or achieving something, especially in relation to a particular activity.” If the activity is concerning a soldering process, such a failure can have a downstream impact far beyond the actual solder joint. In this regard, it is first necessary to understand what constitutes a good solder joint because appearance is too often deemed a success.
These challenges to solder joint reliability were exemplified when, in July 2006, the RoHS directive came into effect, and the higher thermal demands of lead-free solders forced all manufacturers of soldering irons to focus on improved heat transfer. This requirement was further complicated by the ongoing decrease in component sizes and the fact that many PCBs are becoming more like heat sinks due to multiple layers and other factors. The importance, therefore, is for soldering irons to provide:
- A fast response (speed)
- No overshoot (control)
Certainly, most systems today offer good or even excellent performance in thermal energy capability, but difficulties emerge in those systems using conventional ceramic heater technology, especially concerning:
- Tip-to-ground resistance (difficult to maintain)
- Tip-to-ground voltage leakage (difficult to maintain)
- Thermal transfer efficiency
- The potential for solder splatter (due to temperature overshoot)
- A requirement for calibration of the thermocouple
In this article, we will explore the considerations necessary to achieve good solder joints and offer some practical rules for good solder joints and how to achieve them reliably. We will also discuss other thermal energy factors to keep in mind.
Figure 1: Components of a good solder joint and their relative placement during the creation of a solder joint.
The considerations necessary to achieve good solder joints are (Figure 1):
- The formation of an intermetallic layer
- Solder joint structure
- Joint temperature (military standard)
- Tip temperature vs. joint temperature
- Maintenance of the soldering profile (similar to that found in a reflow oven)
When copper comes in contact with molten solder, it forms two distinct intermetallics between the copper and the tin contained in the solder (Figure 2):
- Layer of “e-phase” (Cu3Sn) next to copper
- Layer of “h-phase” (Cu6Sn5) a thicker layer above
Tin is depleted by the formation of intermetallics, so in tin-lead solders, there will be a resultant lead-rich region.
Page 1 of 2
Suggested Items
Taiyo Circuit Automation Installs New DP3500 into Fuba Printed Circuits, Tunisia
04/25/2024 | Taiyo Circuit AutomationTaiyo Circuit Automation is proud to be partnered with Fuba Printed Circuits, Tunisia part of the OneTech Group of companies, a leading printed circuit board manufacturer based out of Bizerte, Tunisia, on their first installation of Taiyo Circuit Automation DP3500 coater.
Vicor Power Orders Hentec Industries/RPS Automation Pulsar Solderability Testing System
04/24/2024 | Hentec Industries/RPS AutomationHentec Industries/RPS Automation, a leading manufacturer of selective soldering, lead tinning and solderability test equipment, is pleased to announce that Vicor Power has finalized the purchase of a Pulsar solderability testing system.
AIM Solder’s Dillon Zhu to Present on Ultraminiature Soldering at SMTA China East
04/22/2024 | AIMAIM Solder, a leading global manufacturer of solder assembly materials for the electronics industry, is pleased to announce that Dillon Zhu will present on the topic: Ultraminiature Soldering: Techniques, Technologies, and Standards at SMTA China East. This event is being held at the Shanghai World Expo Exhibition & Convention Center from April 24-25.
AIM to Highlight NC259FPA Ultrafine No Clean Solder Paste at SMTA Wisconsin Expo & Tech Forum
04/18/2024 | AIMAIM Solder, a leading global manufacturer of solder assembly materials for the electronics industry, is pleased to announce its participation in the upcoming SMTA Wisconsin Expo & Tech Forum taking place on May 7 at the Four Points by Sheraton | Milwaukee Airport, in Milwaukee, Wisconsin.
Hentec/RPS Publishes an Essential Guide to Selective Soldering Processing Tech Paper
04/17/2024 | Hentec Industries/RPS AutomationHentec Industries/RPS Automation, a leading manufacturer of selective soldering, lead tinning and solderability test equipment, announces that it has published a technical paper describing the critical process parameters that need to be optimized to ensure optimal results and guarantee the utmost in end-product quality.